5 Lessons I Learned from My Experience in Healthcare Packaging
“Personal development is your springboard to personal excellence. Ongoing, continuous, non-stop personal development literally assures you that there is no limit to what you can accomplish.” – Brian Tracy
In the past 18 years of my career, I have been blessed with gratifying opportunities to learn, grow, and foster my knowledge in healthcare packaging. During this time, I worked with some very knowledgeable folks on unique challenges that have allowed me to establish a strong foundation of operating. From working with test methods in a packaging lab to remediating and establishing the packaging function from the ground-up, no knowledge and progression came without obstacles, failures, and lessons. In this article, I will summarize a few of these very important lessons that may help individuals be successful in their roles.
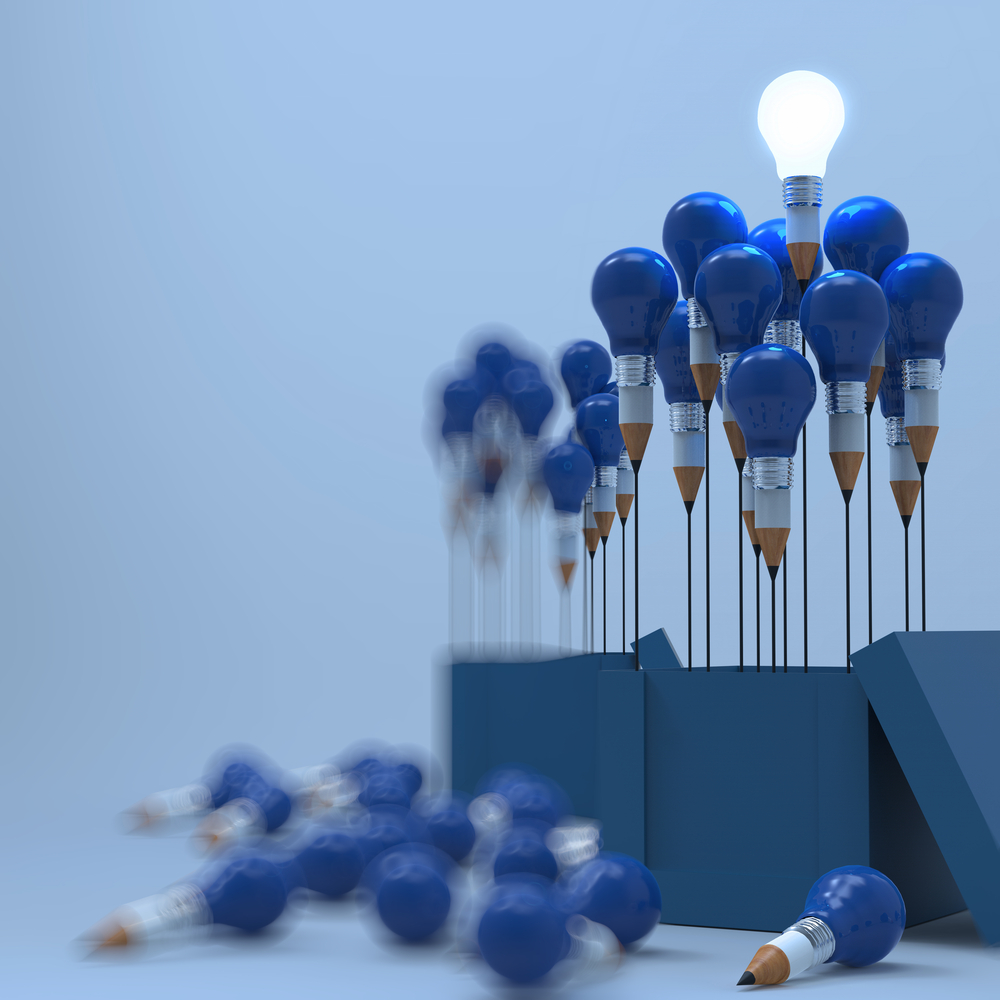
Lesson 1 – Patient first – Packaging plays an integral part in keeping patients safe and delivering the product in its form of intended use to end-users. It is easy to recognize the deep impact we have on our patients from material compatibility, maintenance of sterile barrier integrity, and preservation until the point of use. Ironically enough, under project and timeline pressures, a packaging engineer may be required to grandfather equipment, materials, and designs to deliver rather quickly. However, making rapid decisions can result in oversights affecting the quality of the products. To help create a balanced and focused mindset in such situations, ask yourself – what is the residual risk? Does this adversely impact the patient, compliance, or business? Such risk-based decision making can unearth downstream risks that may not be visible right away. Recognizing if there are patient or compliance risks will allow not only for sound decision making but also help in challenging the status quo, ultimately building trust and credibility.
Lesson 2 – Packaging engineering is not only packaging engineering – Just weeks into my new job as a co-op, it became obvious that a healthcare packaging engineer is not just a packaging engineer. It’s a job of a project engineer & innovator, someone who needs to find a complex balance between addressing user needs, innovation, speed to market, compliance, quality, supply chain, manufacturing, cost, and quality. Touching every single function and each part of the product lifecycle—it is a daunting task to satisfy all customers (internal and external) at once. A good example of rather complex, seemingly simple, packaging is the development of tamper-evident seal labels. Typically, these need to be highly compliant with quality components that are easy to apply during manufacturing and should hold up to a rigorous distribution environment while still being easy to recognize and opened by customers. This is not an easy task to accomplish. Apart from technical aspects, a packaging engineer is also a leader, communicator, regulator, negotiator, and collaborator with all cross functional team members…often an unsung hero who contributes significantly to the safety and efficacy of healthcare packaging.
Lessons 3 – Using knowledge of standards to create wins – Tying back to my earlier comment on grandfathered approaches and being under pressure to deliver quickly, there can be situations where a packaging engineer may be asked to either skip a certain test because it will take too long, or to reduce sample size because it is getting too expensive. In another example, the project team may not know about worst-case sealing conditions or worst-case sterilization for packaging testing and may omit them inadvertently from the plan. There are several ways to educate & persuade and there is no replacing the standards-based approach. Every healthcare packaging engineer needs to be well-versed on industry standards, take time to educate their fellow teams on requirements, and plan appropriately as part of project timelines. Not only does such an approach help create wins, but it also amplifies strong SME experience and credibility.
Lesson 4 – Challenge the status quo – Grandfathering may be a great approach for speed to market, but in hindsight, it may limit the opportunity to serve current user needs accurately and foster organic innovation. The packaging function needs to be Involved early in the design process, whether by internal procedures or via proactiveness. It is imperative to challenge product development teams to create room for advanced engineering & innovation at the concept stage. Getting closer to the end-user and utilizing material, design, and process-based innovation can build a path to a competitive advantage.
Lesson 5 – Fail early, fail often – One of my bosses used to tell me that ‘we never have time do it right, but we always have time to do it all over again’. The comment meant many things to me on a personal basis but one of my key takeaways was to fail early and as often as needed. During your design and development, be sure to perform feasibility tests of all types. From user-based interactions to lab-based worst-case simulations, each test will help lower the risk of last moment surprises and failures. The key here is to proactively plan for time, resources, and cost for such feasibility assessments in your projects upfront.
I truly believe that each opportunity creates a learning that translates into a more effective, sounder mindset. Perseverance, resilience, and creativity are virtues that come in handy in the case of adversities. In closing thoughts, it is important to remember to carry a deep level of gratitude and empathy with the important work we do in serving our healthcare end-users and patients.