6 Healthcare Packaging Materials and How They Reduce Risk
Packaging used for terminally sterilized products in the healthcare industry has one main priority – keep the patient safe by maintaining sterility until the point of use. Common packaging configurations used in this space today (such as pouches, thermoform fill seal or TFFS, lids and trays, and backer cards with pouches) have been designed to meet the needs of a manufacturing and sterilization process, provide product protection through rigorous distribution channels, and allow for aseptic presentation. The materials used in these packaging configurations play an essential role in creating and preserving the sterile barrier system and have evolved over time to reduce patient risk as much as possible.
Paper – Medical grade paper used throughout the industry today is often reinforced with additives (such as synthetic latex or polymer) that provide strength and a clean peel when used in a pouch or lidding application, reducing the risk of fiber generation that could lead to contamination. The paper remains breathable, maintaining the porosity needed for EtO or steam sterilization modalities. This material is particularly useful for light, low profile devices packaged using a TFFS process.
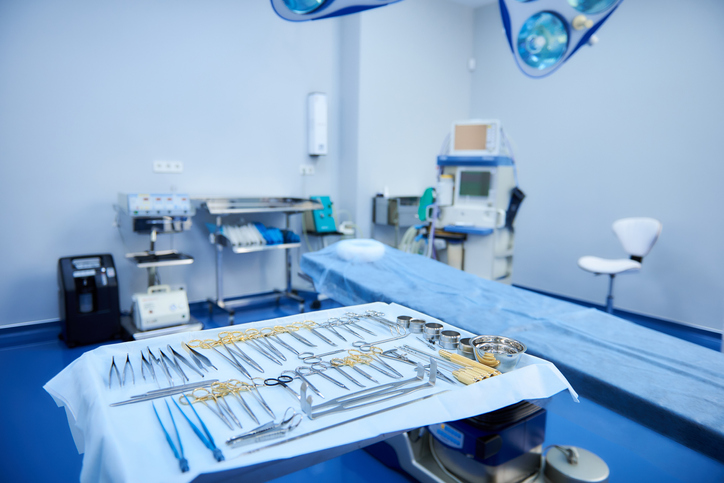
DuPont Tyvek – Tyvek is perhaps the most well-known material used for sterile packaging in the healthcare industry, and for good reason. While it looks like paper and offers the same benefit of porosity to support various sterilization modalities, the unique HDPE structure provides additional strength needed for heavier products and yields outstanding resistance to microbial penetration.
Adhesive Coatings – Adhesive coatings are commonly applied to Lids, especially Paper or Tyvek, to allow for heat sealing and peeling to and from a rigid or flexible substrate. But there are additional advantages to using these coatings in Pouch, Lid, and TFFS applications. They mitigate risks related to fiber tear and delamination, further preventing contamination of a sterile product. They also create a uniform peel for easier, more controlled aseptic presentation to the sterile field.
Foils and Barrier Films – Laminates that include an aluminum foil layer, or a clear barrier film layer, offer protection for products that are sensitive to moisture, oxygen, and/or UV light. The use of the aluminum barrier maintains product effectiveness up until the point of use. However, aluminum cannot seal on its own, and these types of laminations can be vulnerable to chemical attacks and flex cracking. To ensure integrity of the sterile barrier, the foil or barrier film layer is sandwiched between protective layers to allow for heat sealing and/or prevent susceptibility to pinholes. Polyethylene is commonly used to achieve heat sealing and protection, and nylon may be added for applications that require additional puncture resistance.
Nylon Films – Laminates that include a nylon layer(s) add strength, puncture resistance, and flex crack resistance relative to the more traditional PET films used in medical device pouching configurations. These characteristics are a solution for heavy, bulky, or sharp devices that could present the risk of a sterile barrier breach. Nylon is available in a variety of thicknesses appropriate for different applications, from as low as 40ga up to the commonly used 100ga. It can also be laminated with foil when both barrier and puncture resistance properties are required to protect both the product and the sterile barrier.
HDPE Cards – Often referred to as “backer cards” or “mounting cards”, HDPE Cards are an alternative to the more traditional tray configuration that can greatly impact the end user as it relates to patient safety. These Cards are custom designed to secure and organize device and device kits, and truly can become part of the procedure. This provides an advantage to healthcare providers in terms of ease of aseptic presentation, speed of access to a device, and organization of a device or kit in the sterile field that prevents a surgical component from falling and becoming contaminated. And just like many other commonly used materials, these cards are compatible with various sterilization modalities.
The packaging design and materials used in those designs work hand in hand to deliver healthcare products safely and effectively. Understanding the purpose and benefits of these materials, in conjunction with following the requirements set forth by ISO 11607, helps us to ensure we are designing packaging that reduces patient risk as much as possible