The War Against Novel Coronavirus
As 265 million Americans across 32 states live under stay-at-home orders, the US economic outlook also darkens in the wake of climbing COVID-19 cases and deaths. While Congress implements an unprecedented stimulus package to ease wage and business losses, both the private sector and government agencies at different levels face yet another Corona-era challenge: supply chain disruptions in vital sectors such as health care manufacturing. Armed with the Defense Production Act, the Trump administration aims to speed up production of items desperately needed by hospitals everywhere. But will this step succeed in addressing shortages in our interconnected, globalized manufacturing world?
Governors facing potential scarcity of ventilators and personal protective equipment for healthcare professionals have urged the Administration to ramp up production. A flurry of starts, false starts, and stops in agreements between the government and auto-makers-turned-medical-device-manufacturers has left the public unclear about what production plans are confirmed and when the equipment will become available. Despite some high-profile dust-ups, it appears progress is underway.
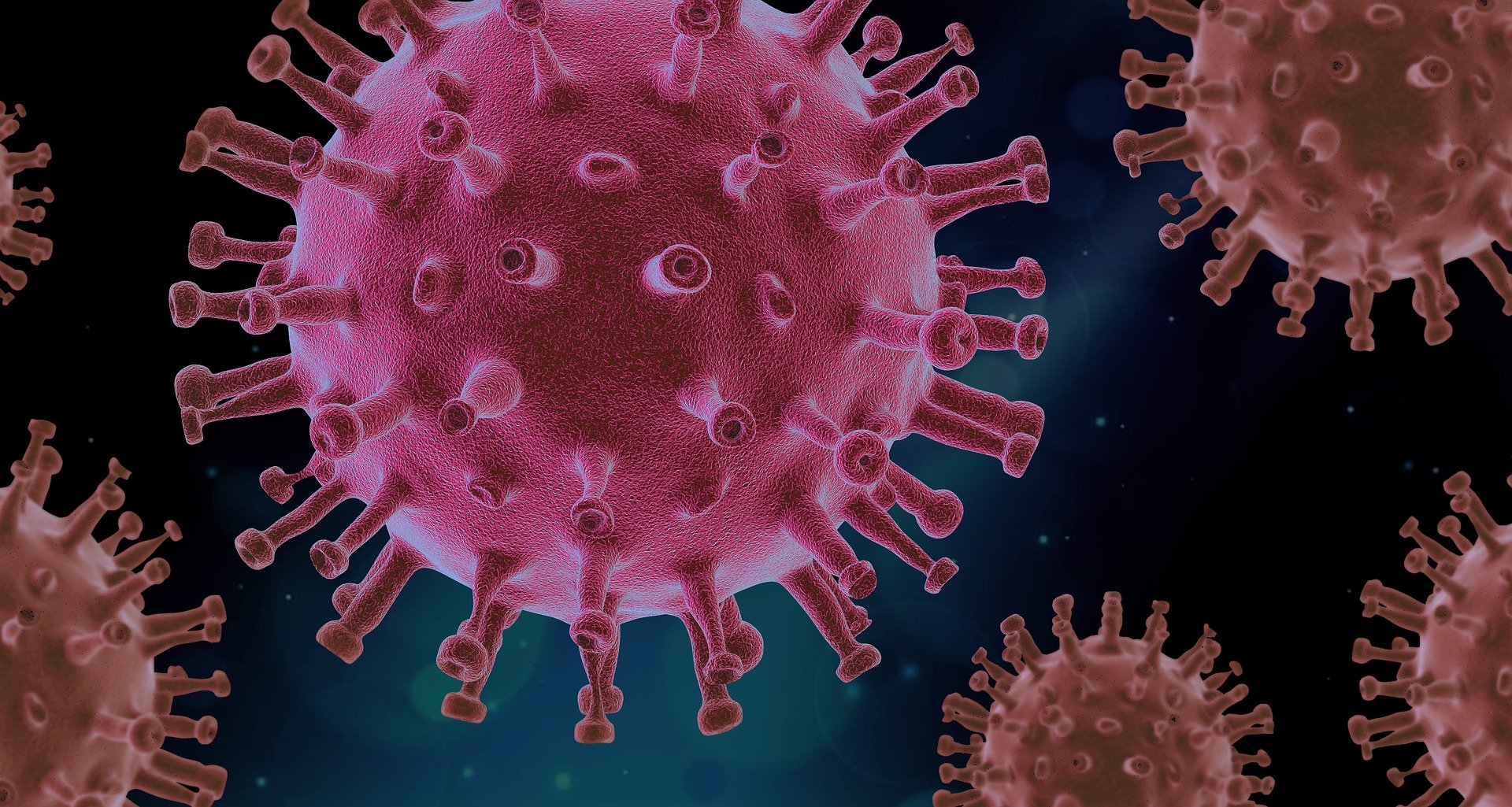
As of Tuesday, March 31, Ford Motor is teaming up with GE Healthcare to produce FDA-approved Airon A-E ventilators for rapid deployment to US hospitals. Its simple design operates on air pressure instead of electricity, allowing for fast production. UAW workers at the Ypsilanti, MI Ford plant expect to build 7,200 ventilators a week, beginning in mid-April. The joint venture hopes to distribute 50,000 of the units by July 4, as part of the Administration’s “100,000 Ventilators in 100 Days” initiative, invoked under the Defense Production Act.
Only called upon a handful of times since its creation in 1950, it is impossible to predict if these efforts or the terms of the law can solve the logistical challenges with our supply chain in a modern and interdependent manufacturing economy.
In addition to the dire need for hospital PPE and equipment, the pandemic has sparked fears of drug shortages. The US relies heavily on pharmaceutical supplies from China and India. Drugs like penicillin and some antibiotics (or their ingredients) are primarily sourced from China. With Chinese manufacturing shut down since early February, with the initial outbreak of the virus, facilities are just now back up and running, according to reports. While our domestic effort may be able to allocate resources, there is little that we can do to influence or predict foreign production levels as the crisis increases need in the US.
Uncertainty over the availability and distribution of COVID-19 test kits has also been a strain across the US. Yet, medical device and pharmaceutical companies across the country continue to offer help where they can. On Monday, March 30, Arizona labs Paradigm and Prorenata announced mass production of coronavirus test kits with 24-hour results turnaround, along with accelerated diagnostic rates to process up to 8,000 daily tests by late April. And on Tuesday, March 31, the FDA approved Bodysphere, Inc.’s serological testing kit with two-minute positive/negative results for COVID-19. Bodysphere’s version joins Abbot Laboratories’ emergency authorization to produce portable testing units capable of detecting the virus in five minutes. Abbott plans to ship 50,000 of the tests daily, beginning this week.
In our current time of crisis, weaknesses, and risks in our traditional supply chain model become increasingly visible. Yet, we also see that our industry's resourcefulness can (and is) bridge gaps. Fortunately, medical manufacturers, packaging partners, and labs are well-versed in not only agility and fast-changing conditions, but also in working with the FDA and regulators to help get things done—and get them done right.
At Oliver, we are committed to supplying medical packaging solutions for the health sector for the fight against COVID-19.
Author: Nam Nguyen, Market Analyst