Comments (0)
Recently Published Articles
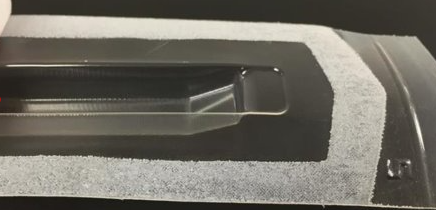
Lid/Tray Seal Watch Outs for Sterile Barrier Medical Packaging
Kevin Zacharias
Regulations and Standards
— 2 minute read
.png)
When and Why You Should Use an Adhesive Coated Material
Jessie Jiang
Education
Regulations and Standards
— 1 minute read
Contact Us
CONTACT US
CHAT