Cold shock failure is a rare problem in the packaging world. During my time as a packaging engineer, I can count on my hand the number of times I have seen this occur—and I’ve only ever seen it take place with rigid thermoformed trays and lids. But let’s take a step back. What is cold shock, or as some call it, cold crash failure? Simply put, it’s a type of failure that occurs when a sterile barrier packaging system is exposed to both extreme cold temperatures and significant shock.
Supply chain channels that include very cold environments are at the greatest risk for cold shock failures. At a basic level, when a rigid tray is impacted with severe shock while at very cold temperatures, the adhesive coated lid can release from the tray flange creating a breach of the sterile barrier. In my experience, when this happens, there is little or no evidence of the adhesive on the tray flange after the lid is removed. The picture below shows what this defect looks like. In a normal scenario, there would be a continuous band of adhesive transferred to the tray flange after the lid is peeled.
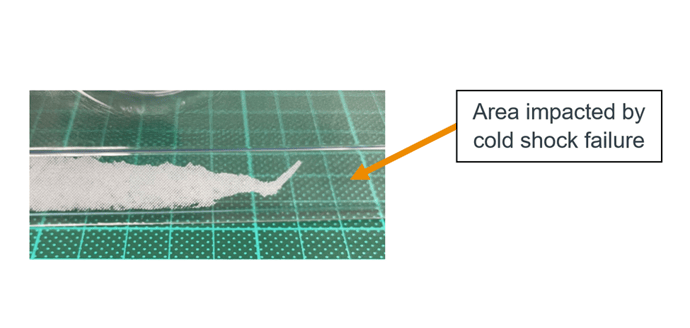
This type of failure is typically very obvious visually. Unlike other failures, such as seal creep and hot tack which can be more difficult to see. Prior to peeling off the lid, you can usually look through the back side of the seal from the underside of the tray flange and see clearly that the bond of the lid to the tray has been compromised (provided the tray material is clear). After the lid is removed from the tray, you can see where the adhesive is released from the tray because it will be on the lid and appear somewhat shiny.
Not all lid adhesives are the same with respect to cold shock resistance. There are a few home-grown tests that can help rank adhesives and their resistance to cold shock failures, but they do not predict outcomes for performance testing. Again, these types of failures, in my experience, are very rare, so to me, it doesn’t make sense to focus too heavily on testing this dynamic.
While cold shock is not a failure I recommend testing for, it is always a good idea to build your knowledge base of potential failures that occur in the field and their root causes.