Healthcare Packaging: Change is the New Normal
It’s no secret that one of the biggest challenges faced by today’s healthcare packaging engineers is change management. The industry is moving faster than ever. Both external and internal forces are requiring packaging engineers to be much more proactive as they consider changes that may impact the packaging system; and all of this comes as international regulatory bodies heighten their expectations of healthcare organizations.
As teams work to define the most effective and efficient ways to manage packaging changes, there is an opportunity to knowledge share across the industry, and to learn from each other’s successes and failures. To encourage this approach, I took the opportunity to sit with members of Oliver’s Technical Services team to brainstorm about the packaging changes they are seeing—and the types of industry change that seem to be most prevalent. I also invited sharing of strategies and best practices to consider along the way.
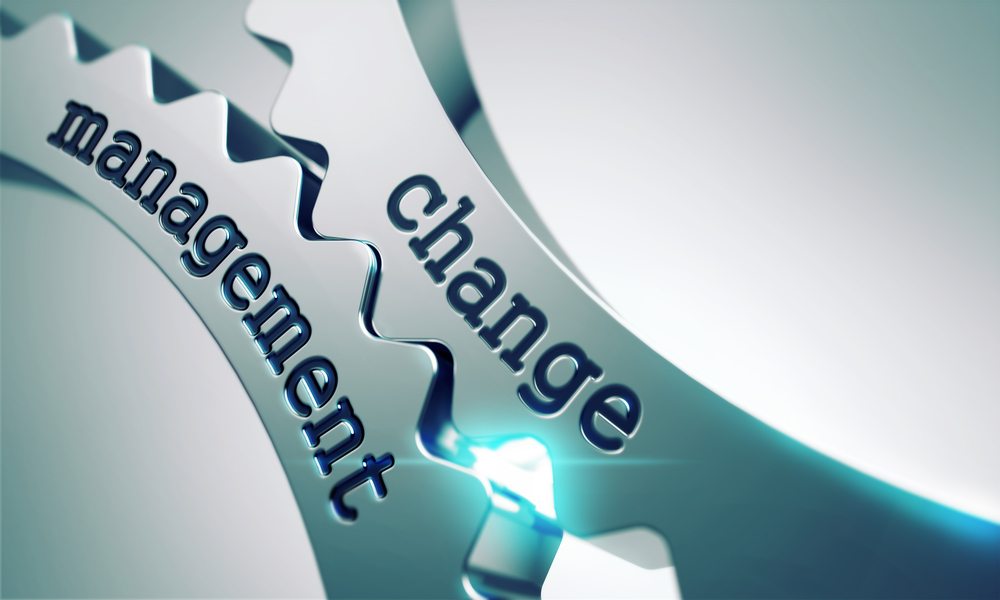
What are the most common drivers you see in the healthcare industry today that result in a packaging change?
-
Kevin Zacharias (Technical Director): Changes are driving changes. Supply chain is the big one right now, as disruptions upstream create a trickle-down effect that is currently unprecedented. There is a need to dual source and qualify materials and components.
-
Geoff Pavey (Technical Fellow): Yes, everyone is looking for alternatives to get past lead time issues, but material changes are also driving the need for finding alternative materials. Ten to 15 years ago there were maybe one or two material changes per year, and now it feels like 50—it seems to have ramped up over time, largely due to upstream consolidation efforts due to economic pressures or even business changes, such as M&A projects. We are also seeing changes to support material reduction efforts for sustainability initiatives.
-
Jeremy Elwell (Senior Principal Engineer): I agree, the biggest current driver of change is within the supply chain. We also see changes initiated by our customer base, such as packaging configuration consolidation efforts.
Are there any industry standards, available now or on the horizon, or best practices that packaging engineers and functional teams can turn to when addressing changes?
-
Geoff: Most customers use some sort of design control practice, taking fundamentals from regulations such as ISO-11607. There is a generally similar approach across larger manufacturers. Depending on the change, you are making sure you are developing the right product and can produce it more than once. Suppliers may offer some guidance to smaller manufacturers or start-ups, but it really points back to ISO change control practices. Managing changes has been a topic for a long time in our industry (what is "significant" vs what is not). However, the topic is coming up again in terms of how to address changes quickly. Committees are renewing focus here to help businesses more uniformly address and manage changes as they come so fast. It’s not about defining change (like it has been historically), but rather, do we have a process that is effective and efficient. So, we may see more here in the future from an industry standard perspective.
-
Jeremy: When undesired changes from the supply chain are forced upon a device manufacturer, they may find it necessary to re-perform some or even all of the packaging design validation testing. I’ve noticed that, in some situations, a decision is made before the scope of the change is completely understood. It may be helpful to work with suppliers to understand the change and then subject it to the design control and risk assessment processes within the applicable quality system. In some cases, a rationale could be written to mitigate the risk and significantly decrease the amount of testing required.
-
Geoff: Suppliers can often provide guidance on how a customer can implement best practices, or how they can leverage documentation to support submissions to regulatory bodies. So, once a customer has completed a risk assessment, a supplier can partner with them to provide insight into what an auditor, notified body, or other reviewer might expect based on similar experiences with other customers.
What strategies have you seen used to help mitigate risks related to packaging changes? What is the most important thing to think about?
-
Jeremy: Patient safety is number one when assessing risk related to change… usability is related to this, as it can impact patient safety, but it really all funnels back to that.
-
Kevin: When I worked at a MDM, we would encourage a customer to dual qualify a product or materials (for example, qualify two similar sterile barrier pouches) so there is a contingency plan.
-
Jeremy: If you are required to perform testing as a result of a change (or any time you’re performing a packaging design validation), do your due diligence first. Perform feasibility studies, preferably to the edge of failure, to fully understand the entire packaging system prior to a full validation. Spending time up front can mitigate risks and save even more time in the long run.
-
Kevin: Really understand your full supply chain to understand where your risks are. This is not a new concept but has obviously been escalated. Customers are deep diving into this more now.
-
Geoff: Be mindful of all the tools available to you within ISO 14971 to complete a risk assessment. Our industry often defaults to FMEA, but that is just one tool. Use these tools to assess what changed, how significant it is, and how that applies to your specific application, to help decide the best path forward to address a change.
Effective strategies for managing packaging changes and mitigating risks associated with change is a cross-functional effort. It requires careful preparation in the product development phase; an early analysis of the supply chain, available materials and contingency plans, and a consideration of the “what ifs”. And when changes inevitably occur, it is key to think before reacting, and to ask yourself several questions. What is the true risk to users and/or patients? What tools should I use to assess risk? What rationale(s) can be utilized to support this change, and how can I lean on my supplier’s or peers’ expertise? And through sharing our change management wins, we provide positive input into future standards and become more efficient packaging engineers, while ensuring the safety of end users and patients.