How A Film-to-Film Packaging Design Can Impact the Results of Distribution Testing
You decide on your medical device packaging and are ready to launch to market, but you discover you have forgotten a key part of getting your device launch – packaging validation
Depending on your timeline, this could be a major roadblock for your product launch. Validation is a necessary step required by the FDA and the only option is to comply and get the ball rolling as fast as possible.
The most important aspect of sterile packaging is that it arrives to the hospital intact and sterile. You never know how a package is going to be handled, so we must test for the worst-case scenario.
In this blog, we will analyze how packaging design can impact the results of distribution testing. Doing this can potentially forecast what failures might occur during distribution testing.
The three tests within the transit testing standard, ASTM Standard D4169, that we will analyze include Drop Testing, Vibration, and Altitude.
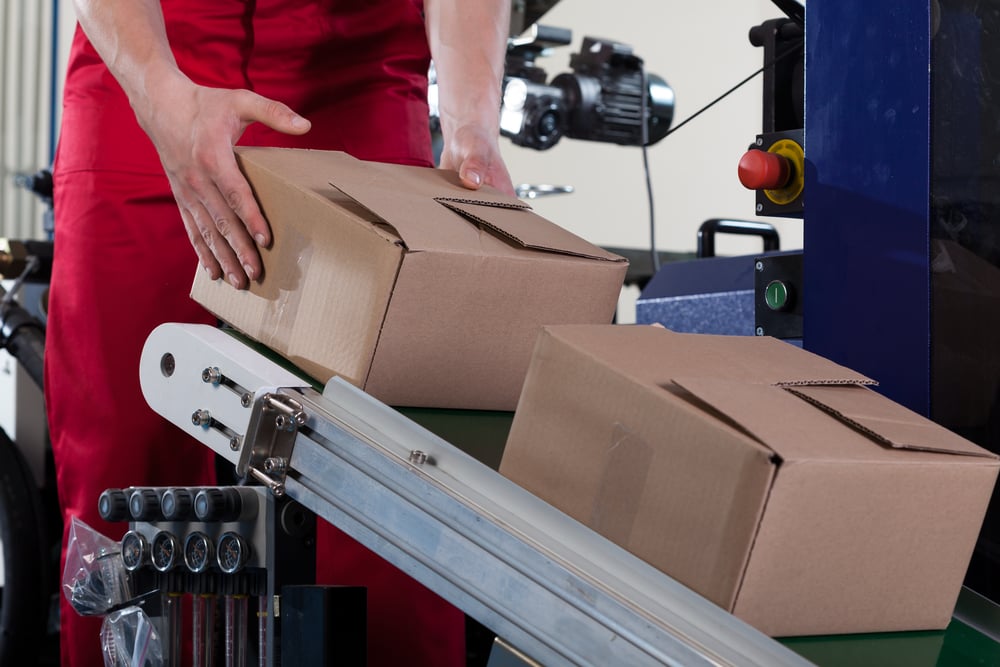
How Does a Film-to-Film Pouch Impact the Result of a Drop Test?
To understand how a film-to-film packaging system can impact the results of a drop test, we first need to understand what the test is meant to do. Drop testing simulates how packaging might be handled during the distribution cycle. We do this by dropping shippers at various angles and heights to make sure the packaging system maintains sterility.
The device is likely to be the reason for failure in drop testing. Under a microscope, these failures will look like the device has stabbed through the pouch. To avoid drop related failures, we would recommend the following:
-
Contain the device with die cut HDPE cards or caps. Sharp features that are uncovered can cause punctures and internal abrasions.
-
Choose a material with a higher puncture resistance.
How Does a Film-to-Film Pouch Impact the Result of Vibration Testing?
Vibration testing simulates what a package will endure while it is in the back of a shipping truck. Since your samples will have to be in a delivery truck at some point of the distribution cycle, we must test to make sure your samples can endure the constant rate of vibration that shippers experience.
The friction from the constant vibration can cause interior abrasions from the device. External abrasions can occur as well if the pouch is not sized correctly. It boils down to the back and forth movement wearing down the material. For this example, let us imagine sandpaper on wood. What happens inside or outside your packaging is the same thing that happens when you use sandpaper on wood. Eventually, the device can rub a hole through the packaging which would allow microbes to enter. This would be a sterile breach and must be avoided.
We would recommend the following to prevent vibration related failures:
-
Be sure the pouch is sized correctly. A good rule of thumb is the device should lay flat in the pouch. When it is sealed, the internal part of the pack should not be taut or tight fitting to the device. When the pouch is snug on the device, it can cause points in the material which can rub against other pouches and create an external abrasion. Similarly, if the pouch is too large, it will not fit in the shelf container properly which creates points in the packaging which can rub up against the shelf carton that houses the device.
-
If the device is causing an internal abrasion, the issue is resulting from poor containment of the device. We can combat this by using a die cut HDPE card to mitigate movement.
-
Be sure there is not too much movement within your shipper. A good rule of thumb is if you shake a shipper and you can hear movement inside, you should add dunnage to the shipper to mitigate as much of that movement as possible.
How Does a Film-to-Film Pouch Impact the Result of Altitude Testing?
Altitude testing simulates what packaging will endure while it is traveling at high altitudes and pressure changes. For example, being shipped via airplane or on a delivery truck driving through the mountains.
Choosing a material that is porous will be your safest bet if your packaging system must endure altitude testing. Where you start to run into problems is when you have foil-to-foil pouch or a foil lid on a thermoform tray. To explain what happens with altitude failures, imagine a bag of chips on a plane. When that bag of chips experiences the pressure changes from high altitudes, it causes the bag to expand. Since the bag material is not porous, the air on the inside keeps trying to push out until the bag pops. This also happens with foil-to-foil and film-to-film pouches at high altitudes if the air cannot pass through the material.
Let’s return to our original film-to-film example. Film material is nonporous and will be affected the same way as foil-to-foil. Failures with film-to-film packaging are rare for altitude testing, however they can happen if the seal is too weak.
If using foil is necessary for your device packaging, do not fret; there is a solution. If you have a vacuum sealer, you can use that to suck the air out of the packaging while you seal it. Doing this would cost more because the sealing equipment will need to have vacuum capabilities which is expensive, but it would ensure your foil packaging will not burst.
Conclusion
The great part about using a testing expert like PCL is that we have medical device packaging specific engineers on staff who can come up with solutions for your packaging before it goes through transit testing. This will ensure that you are less likely to encounter failures and can get your device to market on schedule.