How to Approach Curving or Coiling Long Catheters
Long catheter systems can be a complicated problem when it comes to package design. As the name suggests, they are long and awkward to handle for manufacturing personnel, storage facilities, and end users. Considering alternative packaging configurations, such as curving or coiling the catheter, is an opportunity to simplify the user experience and gain efficiencies throughout the product life cycle. I recently discussed this topic with Vipul Rajpara, a Packaging Leader at Edwards Lifesciences with 15+ years of experience, much of which has been dedicated to long catheter packaging development. He is knowledgeable and passionate about the cross-functional proficiency needed by Packaging Engineers to succeed in this space. Here are some things he recommends considering when approaching package development.
1. Always start with the user experience and patient outcome
Product performance, end user impact, and patient safety are top priority when it comes to designing and developing catheter packaging. Because catheters are delivery components that typically connect to other devices, it is essential to understand the complete preparation procedure in the operating environment to identify areas for improvement.
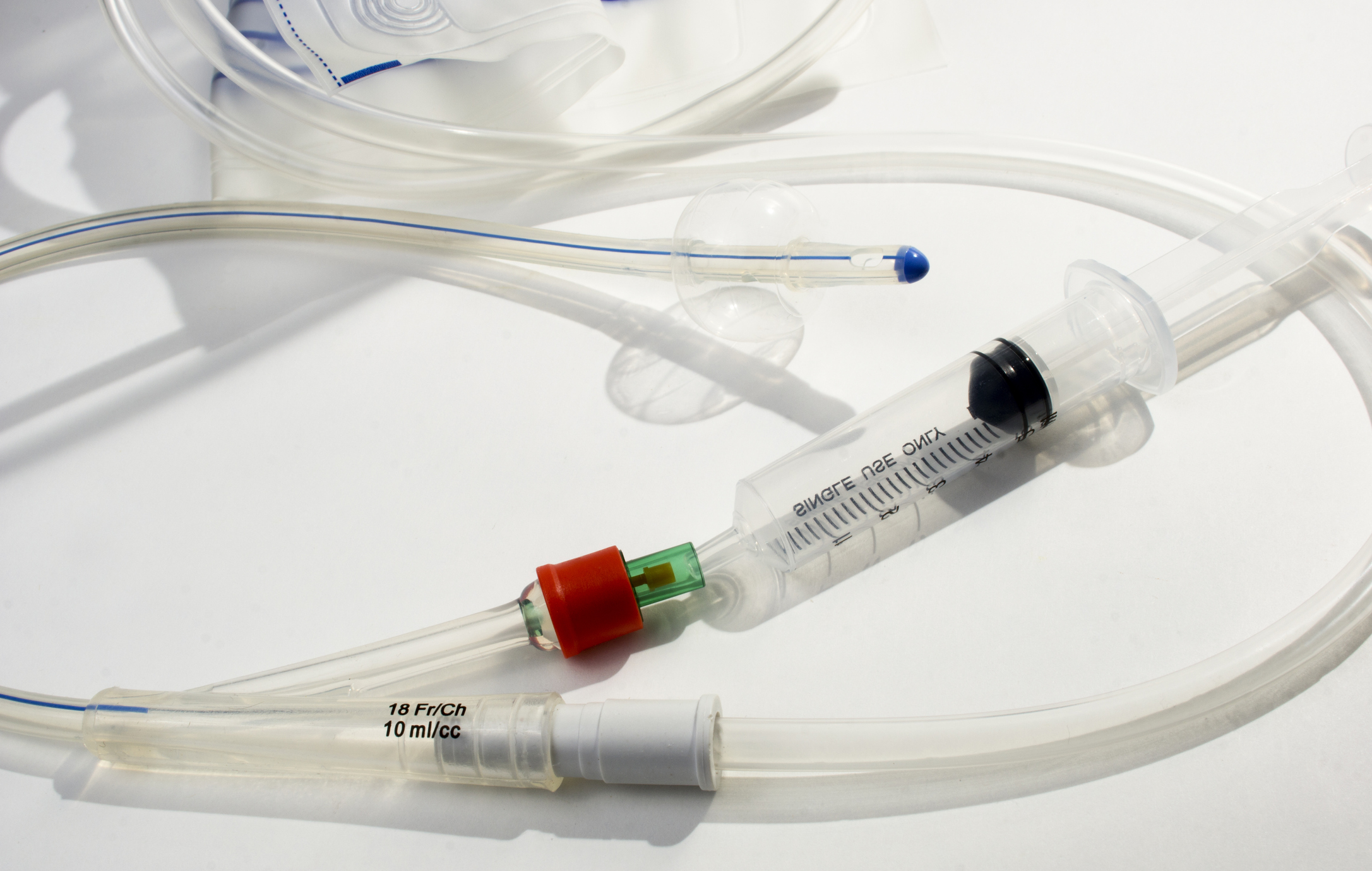
By curving or coiling the catheter within the package, is there an opportunity to reduce prep and procedure time (which in turn positively impacts the patient) or even eliminate an entire prep table? Could the package design also reduce the number of personnel needed, or aid in final device connection? It is vital that this information ultimately feeds into the design and user requirements upstream; gathering this intel and sharing it with the product design team can influence the actual catheter design and material, ensuring there is no compromise in product performance while also achieving optimal package design. A collaboration between product design, packaging, and the customer is the ultimate win/win scenario to achieve upstream influence.
2. Consider and assess operational impact and cost savings
As mentioned above, when it comes to designing medical device packaging, the end user and patient safety requirements are your starting point when considering a new configuration. But the impact throughout the operational and shipping environments are essential to assess and can act as a helpful change agent when influencing internal stakeholders. Remember, these are long and often awkward devices to handle; a curved or coiled configuration can lead to easier assembly/labor savings, increased productivity, and considerable space savings. There will also likely be packaging material cost savings, and a positive impact to shipping and storage of both the packaging components and finished packaged device (also leading to sustainability related benefits). And don’t forget about sterilization requirements… could a straight configuration even fit in the intended chamber? Partnering with operations early in the development process to quantify these savings and efficiency gains will help influence design requirements now and later.
3. As a packaging engineer, your focus must go beyond the package
Per Vipul, “when developing this system, you need to wear multiple hats and think 360˚ to get the results and create a win/win situation”. This takes practice, but by affording yourself the time to truly watch and learn the problems being faced by both internal and external customers, and then connecting and educating functions to influence device and package design criteria early on, you can make a significant impact to your organization and patients while also carving best practices for future device generation development. This is especially true in a space like long catheters where, from the end user’s perspective, the package may truly be a part of the product.
Vipul is not exaggerating when he says long catheter packaging development (and really all healthcare packaging development) “takes a village”. It’s a back-and-forth process between device and package design teams, as well as internal and external customers, whereby the device and package will take on alterations simultaneously. While this may sound chaotic, being prepared and informed can result in a form of organized chaos that is well worth the effort.
If you would like to learn more about catheter packaging, click here!