Understanding the Differences Between Cast and Blown Extrusion in Film Production
In the world of plastic film production, two predominant methods stand out: cast extrusion and blown extrusion. Both techniques play crucial roles in various industries, including medical and pharma packaging. They have some differences in their processes, properties, and their applications. This article delves into these differences and explores how each method is used in the context of healthcare packaging.
Extrusion Process
For both extrusion methods the process starts with melting plastic resins in the extruders. For cast extrusion the molten plastic is rapidly cooled on chilled rollers, solidifying into a thin, flat film.
Blown extrusion involves extruding molten plastic through a circular die to form a tube. Air is then vertically blown into the tube, expanding it into a bubble. In this inflation process the bubble is simultaneously stretched longitudinally (along the length of the bubble) and somewhat transversely (across the width of the bubble). This causes a biaxial orientation of the film. At the top of the machine, the bubble is cooled and collapsed into a flat film.
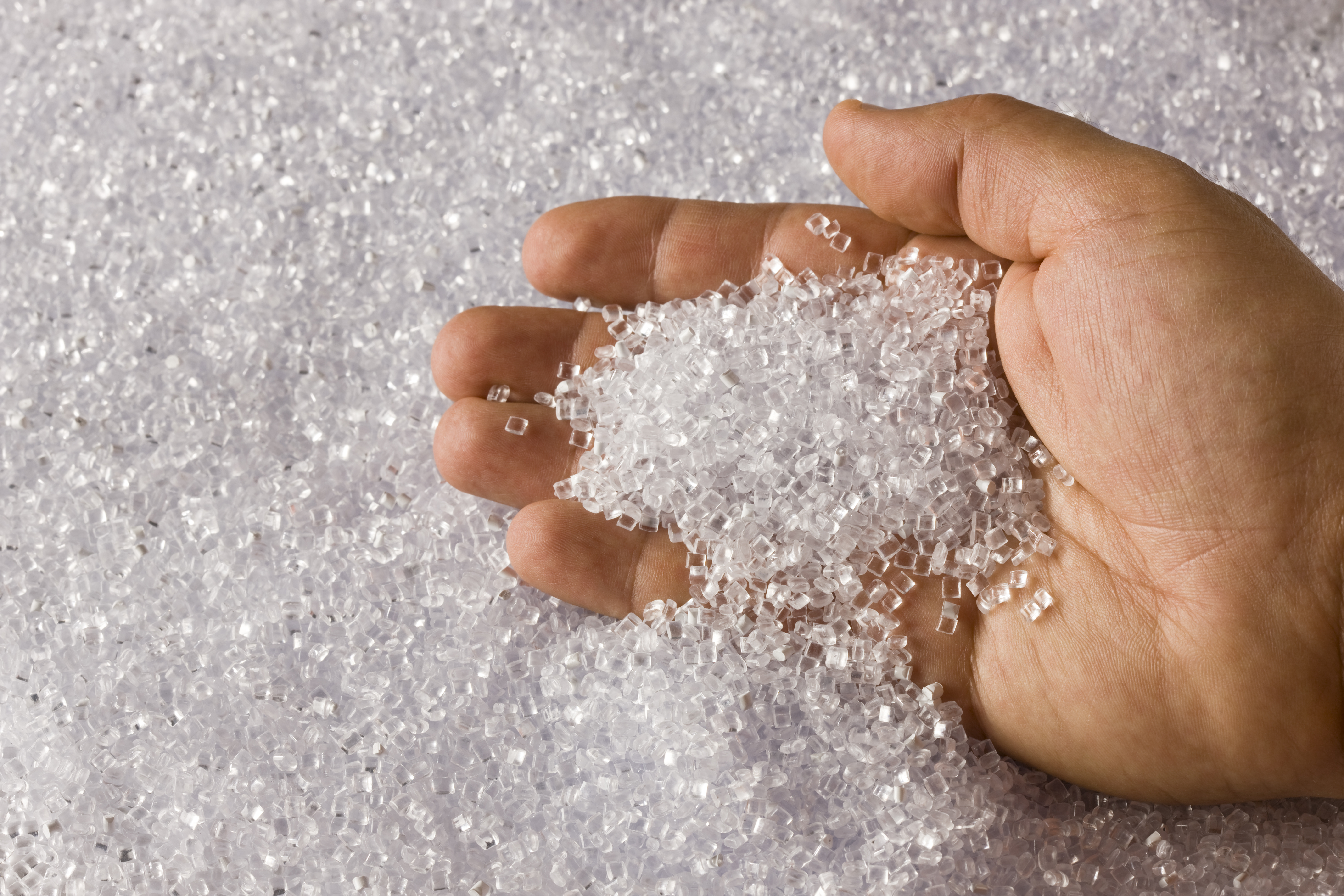
Property Comparison
Both processes can be used to make the same film structures such as PA (Polyamide), PE (Polyethylene), and EVOH (Ethylene Vinyl Alcohol), but there are some differences in the properties of the film that might make you choose a certain extrusion method over the other. One is not necessarily better than the other, but based on your preferred properties you might lean towards either a cast or a blown extruded film.
For example, cast extruded films are known for their excellent clarity and gloss, which is a result of the rapid cooling process. Blown extruded films use a slower cooling process, that results in a hazier film.
Regarding thickness uniformity, cast extruded films stand out due to their highly uniform thickness. Blown extruded films can have slight variations in thickness, although modern technology has significantly minimized this issue. Thickness uniformity is important in films used for healthcare packaging because it ensures consistent barrier properties across the entire film, which is essential for maintaining sterility and protecting medical devices and pharmaceutical products from contamination. Uniform thickness also guarantees reliable mechanical strength, reducing the risk of tears or punctures that could compromise the integrity of the packaging.
Flexibility is an area where blown extruded films have an advantage. They are more flexible than cast films, making them more suitable for applications that require high mechanical stress tolerance. Furthermore, blown films can be made thinner while maintaining their strength and flexibility, this can lead to cost savings due to reduced material usage without compromising performance.
Applications in Medical Packaging
Both extrusion methods have the ability to create films that can be used in medical or pharmaceutical packaging.
Cast films are typically found in:
- Forming Film Applications: Cast films are often used in forming film packaging due to their clarity and deep draw capability.
- Sterile Barriers: The uniform thickness and good barrier properties make cast films suitable for sterile barrier systems that use pouching films or top web films.
- IV Bags: The strength and clarity of cast films make them ideal for IV bags, where visual inspection of the liquid is crucial.
Blown films are typically found in:
- Pouches: Blown films are commonly used for medical and pharmaceutical pouches due to their superior strength and puncture resistance, ensuring the safety and integrity of the contents.
- Wrapping Materials: Their flexibility and toughness make blown films ideal for wrapping sterile instruments and supplies.
- Laminating Films: Due to their superior strength and flexibility, blown films are used for laminating in either extrusion or adhesive lamination. Their good barrier properties, combined with modern advancements in thickness uniformity, make them ideal for creating robust, multi-layered laminates in packaging applications.
Both cast and blown extrusion methods offer unique advantages and are chosen based on the specific requirements of the application. In medical packaging, the choice between cast and blown extruded films depends on factors such as clarity, strength, and flexibility. By understanding the distinct characteristics of each extrusion process, manufacturers can better meet the stringent demands of medical packaging, ensuring the safety and efficacy of medical products. Whether it's the high clarity and uniformity of cast films or the superior strength and flexibility of blown films, both technologies play an essential role in medical packaging solutions.