6 Types of Application-Based Testing and Why They Matter
Many packaging engineers in the healthcare space are familiar with supplier material data sheets, and the “typical” characteristics and standard material test results commonly found in these resources—attributes such as basis weight and thickness, tensile strength, elongation, and oxygen/moisture transmission rates. These results can be helpful when trying to get an initial understanding of a material’s compatibility with a certain application, or for comparing two or more materials at a high level. However, there are other tests in our industry that are being used more and more to better understand how a material and final package will perform in a real-life scenario, or to troubleshoot performance test failures. Here, we will explore a few of these tests; why they matter, and what they might indicate in terms of true application and the ability of a material or sterile barrier system to withstand the full operational, sterilization, and distribution environment.
Films:
Puncture Resistance: This test will indicate the force required to puncture a film and is typically performed from both the outside and inside of the film. This is particularly important when packaging a device with sharp points or edges. To avoid a puncture failure during performance testing, choosing a film with an appropriate puncture resistance to withstand both the device and any external risks is key.
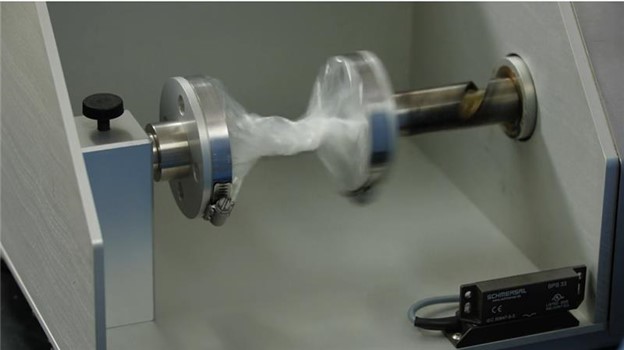
Gelbo Flex Durability: Flex cracking can occur when a film is repeatedly “flexed” or “crinkled” in a particular spot, often during transportation, which can lead to the creation of a pinhole in the film. A Gelbo Flex test will provide insight into a material’s resistance to this failure and provides the ability to rank films. Interesting to note—when it comes to flex crack resistance, thicker material does not necessarily mean better!
Abrasion: Abrasion resistance testing measures the number of times a weighted stylus can be rubbed against a film before it wears through the material. Abrasion failures can be initiated from the outside of a package, due to a “tent” or “fold” in the film that is continuously rubbing against a shelf carton or shipping carton. These types of failures can also be initiated from the inside of the package due to the device abrading the film. Depending on the device and pouch design, this test can help indicate what film structures are most appropriate.
Coated Tyvek:
Elevated Temperature & Humidity Creep: This test will provide insight into the impact of elevated temperature and humidity on an adhesive coating as it relates to seal strength, and can help rank coatings with respect to risk of seal creep during EO sterilization. Seal creep can occur due to a combination of stress on the seal and potential weakening of the coating at elevated temperature and/or humidity.
Hot Tack: This test measures seal strength immediately after heat sealing, prior to cooling to room temperature. This is particularly relevant to sterile barrier systems that are made using TFFS (thermo-form-fill-seal) equipment as there can be stress on the seal during the intermittent motion process and prior to the heat seal coating coming to full strength post sealing. Certain adhesive coatings can fail depending on the sealing temperature, machine acceleration dynamics, weight of the device and other factors. This test will help rank adhesive coatings and forming film combinations with respect to their hot tack characteristics and sealing temperatures used.
Cold Temperature Performance: We are often focused on the effects of elevated temperature and humidity on seal strength in our industry, but performance of materials at cold temperatures and understanding any inherent risks should also be considered. Materials can become brittle at low temperatures, and when exposed to stress/shock, can fail in the form of open seals and cracked substrates. Cold shock failures are typically seen with sterile barrier systems comprised of rigid thermoformed trays and lids as opposed to flexible systems. Methods ranging from flexing sealed films and coated Tyvek that have been exposed to extreme low temperatures to shocking them have been used to rank performance.
There are many characteristics and test results available for commonly used healthcare packaging materials. When reviewing these results or using them to help make design decisions, it is important to understand which ones are useful for high level comparisons, and which ones need to be considered for a specific application and sterile barrier system lifecycle. Take advantage of your suppliers here—ask questions and challenge the status quo to make effective decisions that can streamline your development process!