The Next Decade of Medical Packaging Belongs to China – Part 3
The final part of our three-part series examines China’s role in the global supply chain for medical devices and packaging. A strong central government and experience managing pandemics led the country to a rapid rebound ahead of other economies.
Part 3: Supply Chains Before and After the Pandemic
“This virus knows no border” – was a phrase one probably hears quite often throughout the Covid-19 pandemic. One probably still does now. For many, a double dosage of vaccines and a chance to get back to normal are still at a great distance.
While the pandemic makes the gap between nations seem large, economic globalization has made the world ever smaller. Economists have studied the economic impacts of outbreaks and found most of them to be negative, though short term. This includes the British flu of 1957, swine flu on Australia economy, and AIDS which was suggested to stun economic growth if left to become an epidemic. Surprisingly, empirical data suggests that the 1918 Spanish flu had a positive effect on the economy of the United States.
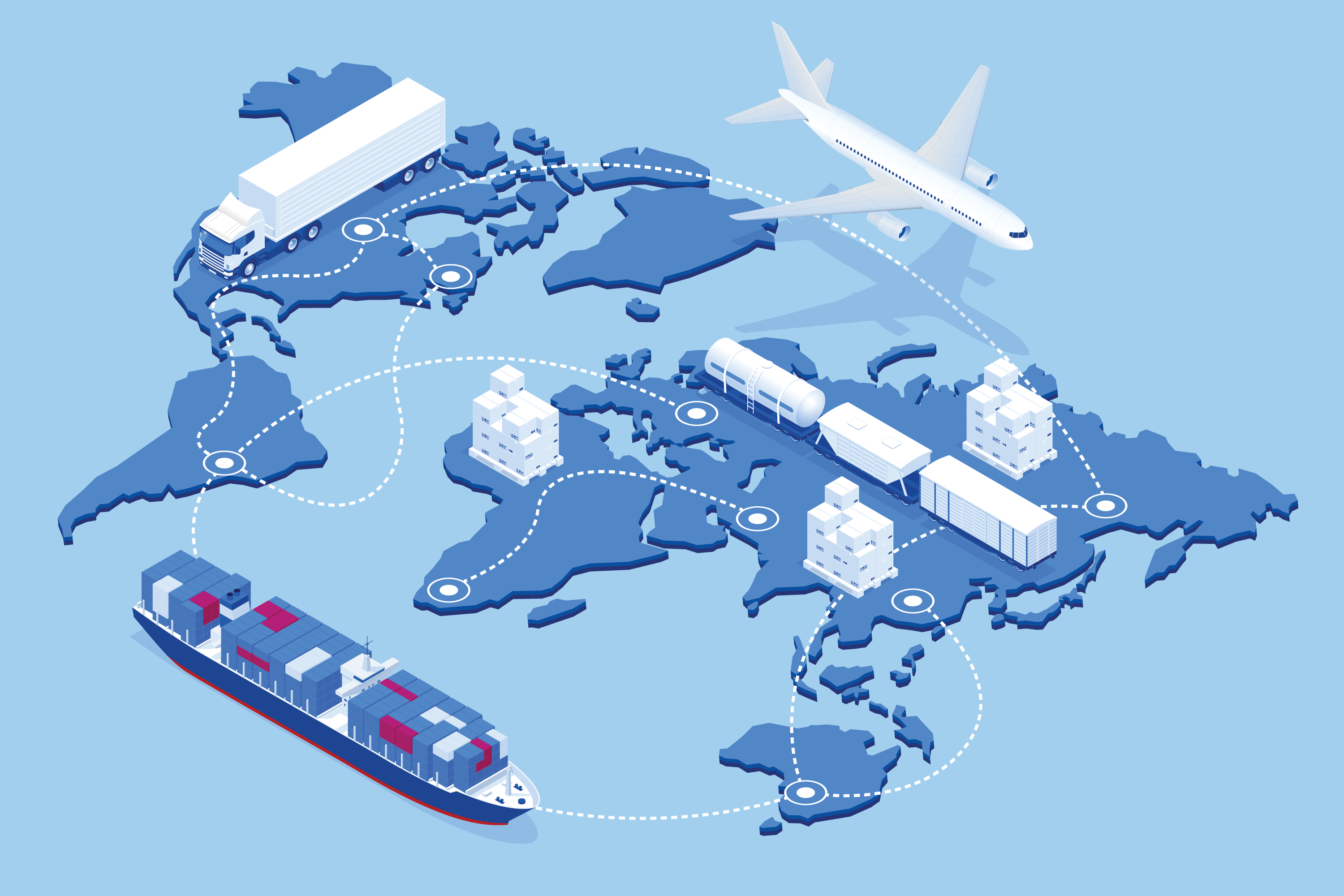
China, of course, felt the massive economic effects that the 2019 pandemic has caused. From the very beginning city closures had worsened its trade environment and halted any progress of foreign investment. In Part One of our series on China, we covered how the country has recently enjoyed robust and raising levels of foreign investment in the medical device space.
But China has shown the ability to manage the epidemic sail itself out of troubled economic waters. Countless studies have found that effective policies and governance play a vital role in lessening economic downfalls and death tolls. Besides its natural ability to govern its population, its exposure to prior pandemics such as SARS contributed to successful pandemic management in provinces such as Guangdong and Henan.
As a matter of fact, there are plenty of room for praises on how the pandemic was handled in China. With its power, public support and cooperation, and economic and diplomatic might, the country was the only major economy that returned to a stable recovery last year. As we covered in Part Two of our series on China, the country was able to quickly mobilize manufacturing assets for vaccine development, as well as accelerate innovation via fast-track approvals. While it turns out Sinovac was later deemed to have a lower efficacy rate, it could be the case that China simply did not have enough affected population to conduct their phase III of the vaccine trial studies, pointing to a rather effective pandemic governance.
Regardless of where one stands on the debate on which approach is more efficient to govern during a public health crisis, one thing is abundantly clear to all: an ever-connected globalized economy exposes all nations to vulnerabilities within the global supply chain. In today’s world, complex manufacturing involves many materials, processes, and countries. A shortage in microchips have caused a delay in automotive manufacturing; similarly, a hypothetical shortage in nucleoside phosphoramidites (key producers being China and South Korea) could easily cause a delay in mRNA vaccine production.
When it comes to supply resilience and reducing global value chain risks, terms like “reshoring”, “regionalization”, and “China+1” entered our discourse of late. But things are not so straight forward. At this early stage, there does not seem to be a mass exodus of manufacturing away from China. Korea, Japan, Germany signal that many of their companies are there to stay, and the Biden administration still has not given any strong signal of a great reshoring.
Localization also became a potential solution for the Chinese domestic market. From semiconductors to medtech devices, bringing different manufacturing streams to China is the strategy for many players and, in the face of supply crunch due to the pandemic or the trade war.
Whether based inside or outside of China, supply chain managers constantly think about mitigation solutions for a more complex and delicate supply chain system. Some have argued that supply chain mapping is a good start for any of the strategies mentioned earlier. In this process, companies spend resources plotting their suppliers (and potentially, second-tier suppliers as well) and conduct what-if analyses to proactively protect supply lines.
While there are still many different challenges that China currently faces to dominate the global manufacturing economy, including the amount of innovation it needs to get to reach technological self-reliance, the country has a lot of advantages that will help own the medical device landscape in the next decade. With a powerful national government, China has the unique ability to push medical technology and improve the regulatory environment much quicker. With growing foreign investments, and as a strong upstream base for manufacturing in pharma and medtech, the nation has a lot of momentum for new breakthroughs as well as sustaining production. And finally, with a governance that quickly learns about pandemic management (as well as other sudden adverse events), China will remain a key player in this industry for the foreseeable future.
Read Part 2: Regulation Speeds Up Due to COVID-19
Read Part 1: Not Just the Low-End Stuff
References: